12 Key Phases in Commercial Warehouse Construction
Thinking about building a commercial warehouse? This 12-step guide walks you through every critical phase, from strategy and site prep to final inspection, tailored for Minnesota’s climate and construction codes.
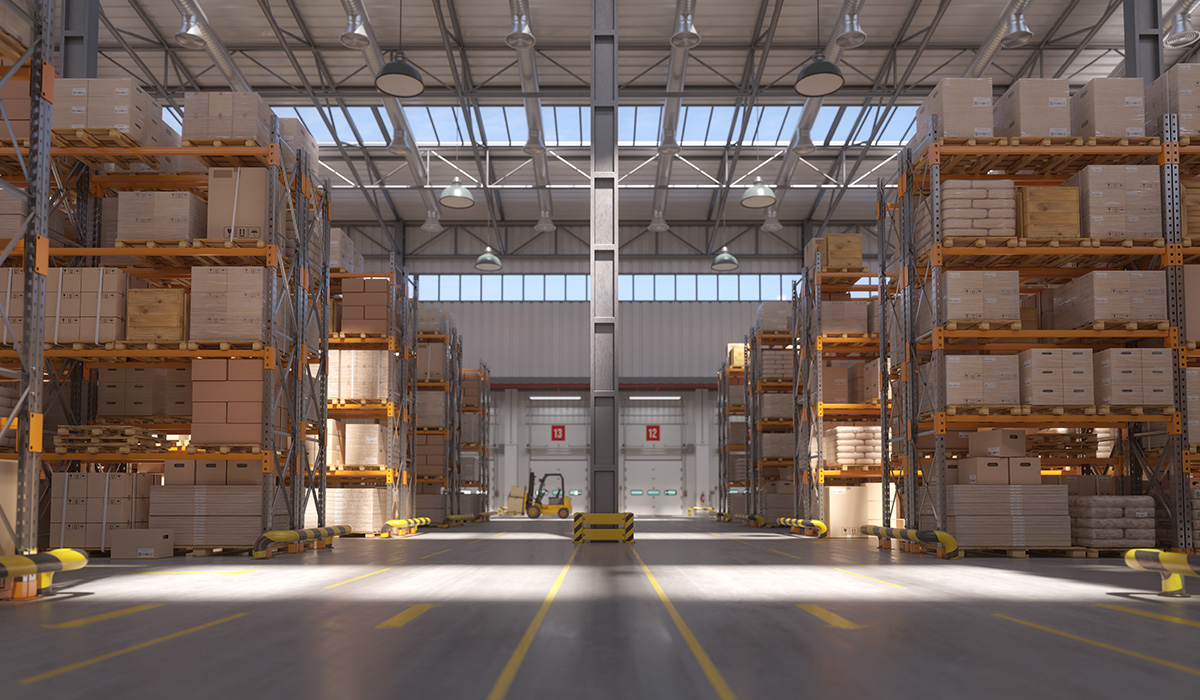
Whether you're expanding operations or launching a new logistics hub, a warehouse is a major investment that demands strategic planning and execution. In Minnesota and the greater Midwest, commercial warehouse construction comes with unique considerations, from weatherproofing against harsh winters to navigating local zoning laws. This comprehensive guide walks you through every phase of the build, ensuring you're fully informed from concept to completion.
1. Why Smart Planning Is Crucial for Commercial Warehouse Construction
Warehouses are the backbone of many industries, whether for inventory storage, distribution, or light manufacturing. But not all warehouse builds are created equal. Successful projects start with a vision and a contractor who can deliver.
At Keystone Design Build, we specialize in commercial construction across Minnesota. Our integrated design-build services streamline communication and keep projects on time and on budget. For clients in the Midwest, we bring insight into local codes, seasonal construction timing, and building for longevity in all types of weather.
2. Start with Strategy: Defining Purpose, Scope, and Budget
Before breaking ground, determine your warehouse’s primary purpose. Will it house heavy machinery? Cold storage? High-velocity e-commerce logistics?
Your answers help define:
- Square footage needs
- Interior configuration (open floor space vs. segmented zones)
- Loading dock and door types
- Energy and utility demands
Quick List: Common Cost Factors in Warehouse Projects
- Land acquisition and prep
- Permit and inspection fees
- Structural materials and framing
- Utility installation (HVAC, electrical, plumbing)
- Custom build-outs and interior finishes
Setting realistic expectations for ROI and upfront costs ensures a smoother process from day one.
3. Location Matters: Site Selection and Preparation Essentials
Your site affects logistics, permitting, and build complexity. When evaluating a potential location, consider:
- Access to major highways and rail lines
- Availability of utilities
- Compliance with zoning and environmental regulations
Warehouse site preparation is critical. In Minnesota, snow loads, soil freezing, and seasonal ground shifts must be accounted for. Proper grading and drainage will protect your investment long-term.
4. Crafting a Design That Works: Functionality Meets Efficiency
Once the site is secured, your design phase begins. At Keystone, we use a Minnesota design-build approach, integrating architects and builders under one roof for better collaboration.
Important elements to consider:
- Clear-span layouts for open movement
- Ceiling height for racking and equipment
- Energy-efficient design (insulation, solar options, natural light)
- Fire exits, sprinklers, and safety zones
Warehouse construction climate considerations in the Midwest include designing for snow shedding, wind resistance, and winter heating loads.
5. Navigating Permits and Pre-Construction Logistics
Permits can slow down even the best-planned projects. Work with a contractor who understands local Minnesota permitting processes.
In this phase:
- Project schedules are finalized
- Materials are sourced and staged
- Subcontractors are secured
- Risk mitigation plans are developed for Midwest weather impacts
This is where having a Midwest commercial building contractor like Keystone on board pays off, we handle the details, so you can focus on business operations.
6. From Dirt to Foundation: Building the Base for Durability
With plans in place, warehouse site preparation begins. This includes:
- Excavation and grading
- Soil testing and compaction
- Installing underground utilities
Minnesota’s freeze-thaw cycle demands a foundation that can expand and contract without cracking. We engineer foundations with deep footings, frost walls, and moisture barriers for long-term durability.
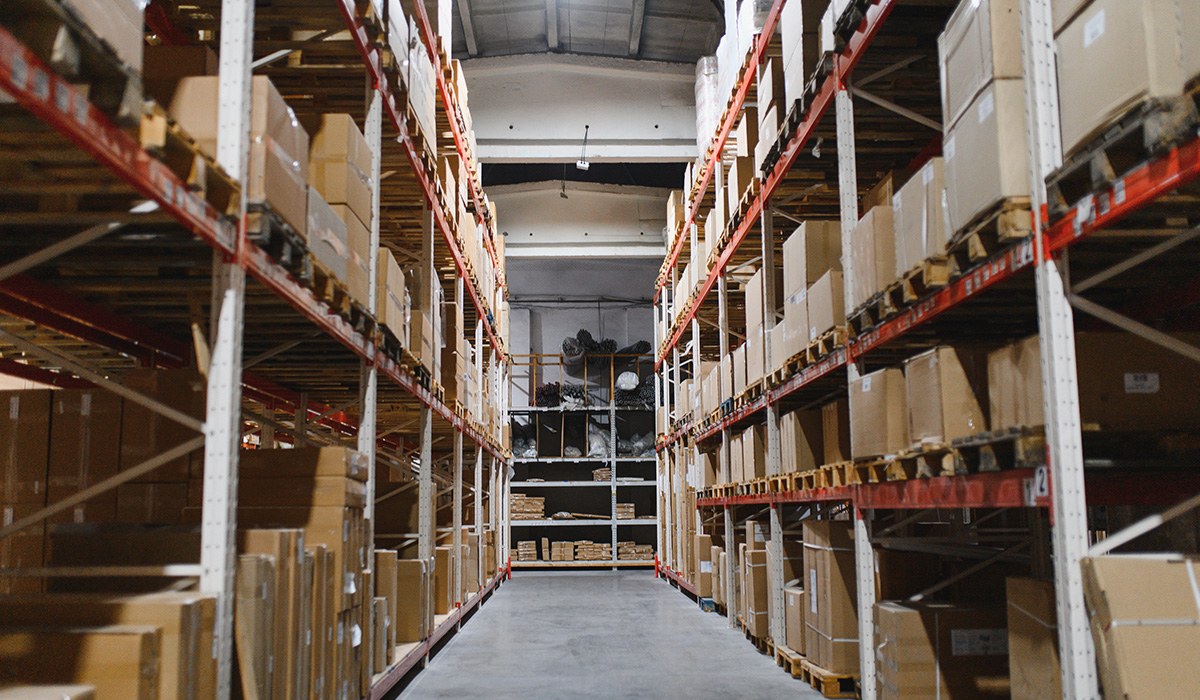
7. Building Up: Framing, Shell, and Structural Systems
Framing options typically include steel or engineered wood. Steel is preferred for large-scale commercial builds due to its strength and flexibility.
We design and install weather-resistant frames that:
- Withstand high wind and snow loads
- Allow for future expansions
- Support overhead cranes or racking systems
Shell completion includes walls, doors, and insulation—all built for resilience.
8. Securing the Envelope: Roofing and Wall Installation
Your roof and walls protect your entire investment, so they need to be tough and efficient.
We recommend:
- Insulated metal panels for superior thermal performance
- Reflective roof membranes to reduce summer cooling costs
- Drainage systems to manage snowmelt
These features reduce long-term maintenance and ensure energy efficiency year-round.
9. Finalizing Interiors: Systems, Safety, and Function
Interior work brings the building to life. Our team installs:
- Electrical systems with smart lighting and power grids
- HVAC tailored to your space and usage
- Plumbing and restrooms
We also ensure full compliance with safety codes:
- Sprinkler systems
- Emergency exits
- ADA accessibility
Custom zones can be built for offices, mezzanines, clean rooms, or climate-controlled storage.
10. Final Steps: Inspections, Walkthroughs, and Ownership
With construction nearing completion, your project will undergo:
- Local inspections for electrical, mechanical, and structural elements
- Keystone-led walkthroughs to address punch list items
- Final cleaning and system tests
Once signed off, we hand over the keys and offer any operational training needed for your team.
11. Long-Term Success: Maintenance and Support Services
Warehouses are long-term assets. Keystone offers post-build support to keep your facility running smoothly.
Maintenance suggestions include:
- Biannual HVAC checks
- Roof and drainage inspections
- Floor and concrete sealant touch-ups
Our team is here for any upgrades, remodels, or expansions as your business grows.
12. Ready to Build? Partner with Minnesota’s Warehouse Experts
From planning and permitting to pouring concrete and final inspection, building a warehouse is a major milestone. When you partner with Keystone Design Build, you get a team that understands commercial warehouse construction inside and out—with local expertise and a commitment to quality.
📞 Schedule a free consultation today or explore our past projects to see how we help businesses across Minnesota grow with confidence.